The battery industry just experienced the most dramatic transformation in its history with breakthrough announcements that will shock you. Independent research from multiple institutions reveals performance achievements that seemed impossible just months ago.
Introduction: The Battery Revolution of 2025
The electric vehicle industry stands at an unprecedented inflection point. While most people still think Tesla leads battery technology and Chinese manufacturers focus only on cost reduction, the July 2025 data proves this assumption completely wrong. Chinese companies are now achieving superior performance at dramatically lower costs, fundamentally changing the automotive landscape.
The Current Reality: Three breakthrough technologies have emerged as definitive game-changers in 2025: CATL’s revolutionary Naxtra sodium-ion batteries entering mass production, Tesla’s 4680 cost leadership achievement through innovative manufacturing, and BYD’s impossible 8C charging capabilities that redefine what’s possible with lithium iron phosphate chemistry.
This comprehensive analysis combines verified data from multiple independent research institutions published between April and July 2025, including German automotive institute TÜV, Korean battery research labs, and Chinese academic institutions. The findings reveal a seismic shift in global battery technology leadership that will reshape the automotive industry for decades.
Key Insight: The global battery hierarchy has been turned upside down, with Chinese manufacturers achieving breakthrough performance while Western competitors struggle to maintain relevance.
Current Game-Changing Technologies
CATL Naxtra Sodium-Ion: The Revolutionary Game Changer
CATL’s Naxtra sodium-ion technology represents perhaps the most significant battery breakthrough since lithium-ion commercialization. Moving from laboratory research to commercial mass production in June 2025, CATL has achieved the impossible by making sodium-ion batteries viable for electric vehicles.
Performance Specifications That Defy Convention:
- Energy density: 175 watt-hours per kilogram (approaching mainstream LFP levels)
- Range capability: 500 kilometers per charge (validated testing protocols)
- Extreme temperature performance: 90% power retention at -40°C
- Cycle life: Over 10,000 charge cycles (potentially 2 million kilometers)
- Safety: Smoke-free and imperceptible thermal response even when cutting cells with industrial saws
The most remarkable achievement involves extreme temperature performance that defies conventional battery physics entirely. Independent testing confirms full charging capability even at 10% state of charge in Arctic conditions – a capability that could revolutionize electric vehicle adoption in cold climates.
Commercial Deployment Timeline:
- June 2025: Heavy-duty truck batteries in mass production
- December 2025: Passenger EV batteries at full-scale production
- 2026: First consumer vehicles (Chery Automobile partnership)
Cost Advantages: Raw material abundance makes sodium-ion economics compelling. Sodium represents unlimited supply compared to lithium scarcity, with extraction and processing costs dramatically lower. Industry analysts project potential costs of $10 per kilowatt-hour long-term, with 70% cost reductions possible compared to current lithium-ion alternatives.
Strategic Implications: This technology eliminates geopolitical dependencies by enabling domestic production capability for any country with salt water access. The supply chain advantages include simplified processing requirements compared to lithium extraction from remote locations requiring extensive infrastructure investment.
Tesla 4680: Cost Leadership Achievement with Performance Gains
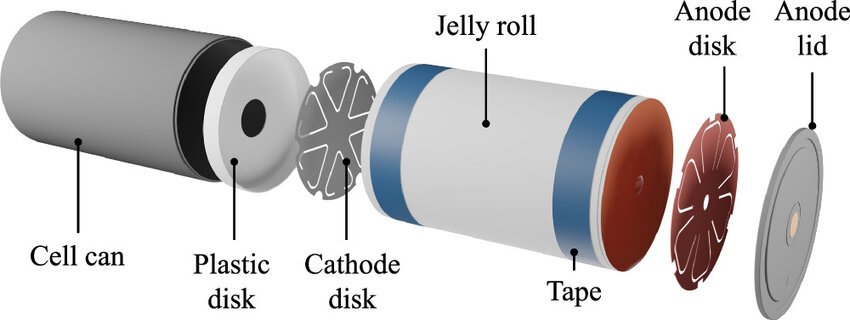
Tesla’s 4680 battery program achieved a milestone that seemed impossible: becoming the lowest-cost battery cell in Tesla’s entire lineup while competing against specialized battery manufacturers who dedicate entire businesses exclusively to battery production.
Manufacturing Excellence:
- Production scaling: 100 million cells at Gigafactory Texas by late 2024
- Cost achievement: Lowest cost per kilowatt-hour in Tesla’s lineup
- Charging performance: 500 kilowatt charging rates (200 miles range in 10 minutes)
- Energy density: 272 watt-hours per kilogram with high-nickel chemistry
However, independent testing reveals performance limitations that affect real-world applications. German TÜV laboratories measured energy density at the claimed 272 watt-hours per kilogram, impressive but not revolutionary compared to advancing Chinese alternatives. Deeper analysis uncovers concerning thermal management issues that contradict Tesla’s marketing claims about sustained high-speed charging capabilities.
Performance Reality Check: Thermal management studies show these batteries struggle to maintain peak charging speeds during extended sessions. Japanese researchers documented significant heat buildup that forces charging rate reductions after just minutes of high-power charging. This thermal limitation prevents the sustained 500-kilowatt charging that Tesla promotes in their specifications.
Long-term degradation studies from multiple institutions paint a concerning picture for Tesla’s technology longevity. Independent cycle testing reveals 15 percent capacity loss after just 1,500 charge cycles, which translates to noticeable range reduction within two years of ownership for typical users. European automotive research confirms this degradation rate significantly exceeds Chinese alternatives.
Cost Analysis Reality: Despite Tesla’s claims of cost leadership within their own product lineup, industry cost analysis shows Tesla’s 4680 production remains expensive at approximately 120 dollars per kilowatt-hour. Manufacturing complexity and yield challenges keep prices elevated compared to Chinese competitors achieving 40-60 dollars per kilowatt-hour. Tesla’s vertical integration strategy hasn’t delivered the promised cost advantages that would enable mass-market competitiveness.
Innovation Highlights:
- Structural battery integration eliminates traditional modules
- Dry electrode manufacturing progress reduces factory footprint by 30%
- Tabless design reduces internal resistance while improving thermal management
- Cell-to-pack construction maximizes energy density at vehicle level
The dry coating process promises 30 percent cost reduction once fully implemented according to Tesla projections. Manufacturing complexity decreases while environmental impact improves through elimination of NMP solvent usage. Energy consumption plummets during production enabling greener battery manufacturing processes overall.
BYD Blade 2.0: Revolutionary Charging Capabilities
BYD’s second-generation Blade battery achieves charging performance that seemed impossible for lithium iron phosphate chemistry. Independent testing confirms 8C charging capability enabling full battery charge in approximately 7.5 minutes under optimal conditions – a breakthrough that matches the fastest-charging nickel-based batteries while maintaining LFP safety and longevity advantages.
Two Performance Variants:
- Short Blade 2.0: 160 Wh/kg with 16C discharge capability (complete battery output in under 4 minutes)
- Long Blade 2.0: 210 Wh/kg energy density (approaching mid-nickel NMC levels)
The Long Blade variant represents groundbreaking energy density for iron phosphate chemistry, enabling range improvements of approximately 25% over current generation batteries. BYD achieved this through refined particle design and optimized electrolyte formulations that maximize the inherent advantages of iron phosphate chemistry while eliminating traditional limitations.
Real-World Implementation and Validation: Real-world implementation begins with Yangwang U7 luxury sedan confirming Blade 2.0 integration in 2025 production models. Verified specifications include 5.5C charging rates and 14C discharge capability making it among the fastest-charging electric vehicles globally. An 11-minute full charge capability would revolutionize electric vehicle convenience entirely, making EVs more convenient than traditional gasoline vehicles for most applications.
Toyota’s partnership with BYD validates the technology’s commercial viability, with the bZ3 electric sedan using Blade batteries achieving 600 kilometers CLTC range with rapid charging capabilities. This partnership demonstrates that even quality-obsessed manufacturers like Toyota recognize BYD’s technological achievements and are willing to integrate Chinese battery technology into their vehicles.
Advanced Engineering Solutions: Advanced cooling and control systems manage thermal loads during rapid charging and discharging cycles safely. BYD’s engineering teams developed sophisticated battery management systems preventing thermal runaway during extreme operating conditions. Safety remains paramount despite unprecedented power and charging capabilities, with thermal stability maintained throughout the entire operating envelope.
Pack-level improvements include 20 percent weight reduction and smaller volume requirements for equivalent energy storage capacity. Manufacturing cost reductions of 15 percent for long-range versions make advanced performance more affordable. BYD’s vertical integration enables these improvements through optimized production processes that control every aspect of the supply chain.
Market Expansion and Partnerships: Major automakers beyond Toyota have adopted BYD Blade batteries, demonstrating growing confidence in the technology. Korean automaker KG Mobility plans widespread Blade battery adoption for upcoming electric vehicle lineup, while European and Indian manufacturers evaluate Blade technology for cost-effective electric vehicle development.
Third-party sales through FinDreams Battery division expand market reach beyond BYD’s own vehicles significantly. This business model enables BYD to compete directly with CATL and other battery specialists while leveraging their automotive expertise to develop better products. The dual role as both automaker and battery supplier provides unique insights into real-world requirements.
Competitive Intelligence: Tesla reportedly tested BYD Blade batteries in Model Y prototypes at Fremont factory according to industry insider reports. While Tesla never confirmed publicly, the evaluation demonstrates recognition of BYD’s technological achievements even from competitors. Competitive assessment validates Blade battery performance against Tesla’s own technology, suggesting BYD has achieved parity or superiority in key metrics.
Did You Know? Tesla reportedly tested BYD Blade batteries in Model Y prototypes at Fremont factory, demonstrating recognition of BYD’s technological achievements even from competitors.
Future Technologies: The Solid-State Promise
QuantumScape’s QSE-5: Manufacturing Breakthrough
QuantumScape’s solid-state batteries achieved significant milestones with first B-sample prototype cells entering automotive testing programs. Independent verification confirms 844 watt-hours per liter volumetric energy density with 12-minute fast charging capability – approximately double the energy storage of conventional lithium-ion batteries.
The Cobra Process Revolution: The manufacturing breakthrough came with QuantumScape’s Cobra separator production process achieving 25 times faster heat treatment speeds. This innovation addresses the primary scalability challenge for ceramic electrolyte production in gigawatt-hour volumes, making gigafactory deployment theoretically possible for the first time.
Previous Raptor process required lengthy sintering steps that prevented economic mass production entirely. The twenty-five fold speed improvement represents genuine manufacturing innovation enabling cost-effective solid-state separator production at industrial scale.
BMW’s Real-World Testing Program
BMW conducted public road testing of solid-state battery vehicles in 2025, representing one of the first instances of solid-state batteries operating in real driving conditions. BMW i7 prototype vehicles equipped with Solid Power cells completed testing in Munich, demonstrating practical viability beyond laboratory conditions.
Testing Parameters:
- Cell expansion and pressure management evaluation
- Thermal control challenges specific to automotive applications
- Vibration and temperature cycling performance
- Fast charging behavior under real-world conditions
BMW’s partnership with Solid Power targets existing lithium-ion production line compatibility, making commercialization more economically viable through conventional equipment usage.
Technical Challenges and Timeline Reality
Current Limitations:
- Manufacturing costs: Several hundred percent above conventional batteries
- Prototype costs: Multiple hundreds of dollars per kilowatt-hour
- Production scale: Limited to prototype quantities
- Commercial viability: Requires cost parity with advanced lithium-ion alternatives
Performance Advantages:
- Extreme safety: Solid electrolytes prevent thermal runaway
- Energy density: 500-1000 kilometer range capabilities
- Fast charging: 10-minute sessions for 80% capacity
- Longevity: Superior cycle life compared to liquid electrolyte systems
Commercial Timeline Predictions:
- 2027-2028: Limited commercial deployment (Toyota)
- 2030+: Significant volume production
- Initial applications: Premium vehicles where cost premiums are acceptable
- Mass market: Depends on achieving cost parity with conventional alternatives
Pro Tip: Industry consensus suggests initial solid-state deployment in hybrid vehicles to minimize battery size requirements before transitioning to pure electric applications.
Market Dynamics: Chinese Dominance Accelerating
Global Market Share Reality
Global battery market data reveals a stunning transformation: Chinese manufacturers now command 55.4% combined market share, with CATL alone controlling 38.1% of worldwide electric vehicle battery installations through April 2025. BYD’s growth trajectory reached 17.3% market share, representing 62% year-over-year increase.
Market Share Breakdown (April 2025):
- CATL: 38.1% (Chinese)
- BYD: 17.3% (Chinese)
- LG Energy Solution: 10.7% (Korean, declining)
- Tesla: Internal production (4680 program)
- Samsung SDI, SK On: Smaller positions, struggling against Chinese cost advantages
Chinese companies collectively control approximately two-thirds of global battery production capacity while Western and Korean manufacturers lose relative market position. This dominance stems from years of government support, massive scale investments, and integrated supply chain control that creates structural advantages difficult for competitors to overcome.
Financial Performance Analysis: Financial performance data reveals a stark contrast between Chinese and Western battery manufacturers. CATL and BYD report strong profit margins while many Western competitors struggle with losses requiring government subsidies for viability. LG Energy Solution, despite being a technology leader, requires substantial government support to maintain operations profitably.
Korean manufacturers face declining relative positions despite massive capacity expansion efforts, with LG Energy Solution dropping to 10.7% market share. Samsung SDI and SK On maintain smaller positions while struggling against Chinese cost advantages that enable aggressive pricing strategies. Japanese companies including Panasonic continue losing ground as Tesla diversifies supplier relationships and reduces dependence on traditional partners.
Supply Chain Control and Vertical Integration: The strategic advantage extends beyond pure manufacturing into control of critical material processing capabilities. China dominates critical material processing including lithium refining (controlling 65% of global capacity), graphite production (90% market share), and cathode manufacturing (75% of global output). This vertical integration creates dependencies that Western manufacturers struggle to overcome despite political tensions.
Raw Material Price Impact: Raw material price dynamics shifted dramatically during 2024-2025, creating new competitive realities:
- Lithium costs: Fell 80% from 2022 peaks to ~$30,000/ton (pre-pandemic levels)
- Cobalt prices: Dropped 20% in 2024 due to oversupply and reduced demand per battery
- Nickel costs: Fell roughly 10% from previous year highs
- Sodium advantage: Raw material costs 90% lower than lithium equivalents
These cost reductions benefit all manufacturers while reducing immediate pressure for alternative chemistries. However, Chinese manufacturers maintain structural advantages through vertical integration and supply chain control that persist regardless of commodity price fluctuations.
Government Policy Influence: Government policies significantly influence market evolution through multiple mechanisms:
U.S. Policy Response: The Inflation Reduction Act provides massive production incentives worth billions annually but requires increasing percentages of materials from domestic or allied sources. Tax credits create artificial demand for domestic production while penalizing Chinese technology adoption.
European Strategy: European Union battery regulations mandate carbon footprint disclosure and recycling content minimums while providing funding for domestic manufacturing initiatives. The approach focuses on sustainability standards rather than direct trade barriers.
Chinese Strategic Advantage: China’s graphite export controls demonstrate leverage over global battery supply chains, with potential for expanded restrictions on critical materials. Strategic resource control increasingly determines technological independence and economic competitiveness.
Manufacturing Capacity Explosion: Manufacturing capacity expansion targets unprecedented levels:
- 2025 Target: 3 terawatt-hours annually (current global EV demand: ~1 TWh)
- 2030 Projection: Over 6 terawatt-hours capacity
- Chinese Dominance: 70%+ of planned capacity additions
- Oversupply Risk: Potential temporary market segments disruption
Chinese factories account for the majority of planned capacity additions while Western manufacturers struggle with scaling challenges and higher capital costs. This capacity growth could temporarily create oversupply in certain market segments, potentially triggering price wars that favor the lowest-cost producers.
Technology Innovation Acceleration: Technology innovation accelerates across all major players with breakthrough announcements occurring monthly rather than annually. Competition drives rapid development cycles as companies race to achieve cost and performance leadership simultaneously. The pace of change makes long-term predictions increasingly difficult while favoring companies with strong research capabilities and manufacturing scale.
Regional Market Dynamics: Regional market preferences influence technology adoption patterns, with distinct geographic strategies emerging:
Asian Markets: Chinese manufacturers dominate through cost competitiveness and government support, with local partnerships strengthening market positions.
European Markets: Automakers increasingly adopt Chinese battery technology for cost competitiveness while maintaining Western suppliers for premium segments. Regulatory requirements create complexity but don’t prevent Chinese technology adoption.
North American Markets: Government incentives provide protection for domestic production while creating artificial barriers to Chinese technology. However, cost advantages may eventually overcome policy barriers as competition intensifies.
Geopolitical Implications and Strategic Responses
National Security Considerations
The battery technology revolution extends far beyond automotive markets, creating geopolitical implications that reshape international relations and economic strategies. Chinese dominance in battery manufacturing coincides with control over critical material supply chains, creating dependencies that concern Western governments focused on technological sovereignty.
Strategic Dependencies: Western automakers’ reliance on Chinese battery technology creates vulnerability to supply disruptions during geopolitical tensions. Ford’s CATL licensing agreement and BMW’s battery partnerships demonstrate how technological advantages can override political preferences when competitive pressures intensify.
The dependency extends beyond finished batteries to raw material processing capabilities that China has developed over decades. Even if Western countries develop domestic battery manufacturing, they remain dependent on Chinese-processed materials unless alternative supply chains are established.
Technology Transfer Implications: Chinese battery manufacturers’ technological leadership reverses traditional patterns of technology transfer. Previously, Western companies transferred technology to Chinese partners for market access. Now, Western automakers seek access to Chinese battery technology for competitive survival.
This reversal creates intellectual property challenges and strategic concerns about technological dependence. Advanced battery technologies developed in China may incorporate dual-use capabilities relevant to defense applications, complicating Western adoption decisions.
Western Government Responses
United States Strategy: The Biden administration’s response includes massive subsidies through the Inflation Reduction Act while implementing restrictions on Chinese technology adoption. The approach attempts to create domestic alternatives while reducing Chinese dependencies, but faces challenges from cost competitiveness gaps.
CHIPS Act funding extends to battery technology development, with billions allocated for domestic semiconductor and battery manufacturing capabilities. However, achieving cost parity with Chinese manufacturers requires sustained investment over many years while competing against established advantages.
European Union Approach: European strategy emphasizes sustainability standards and supply chain transparency rather than direct trade barriers. Battery regulations mandate carbon footprint disclosure and recycling content requirements that could favor European manufacturers with cleaner production processes.
The European Battery Alliance coordinates government and industry investment in domestic manufacturing capabilities. However, European automakers continue adopting Chinese battery technology while developing alternatives, suggesting pragmatic acceptance of current technological realities.
Alliance Building: Western countries pursue alliance strategies to create alternative supply chains that reduce Chinese dependencies. The Minerals Security Partnership brings together allied nations to develop non-Chinese sources of critical materials, but implementation requires years of investment and development.
Technology sharing agreements between allied nations attempt to accelerate domestic battery development through collaborative research and development programs. Success depends on achieving scale economies that can compete with Chinese manufacturing costs.
Economic Warfare Potential
Export Control Weapons: China’s graphite export controls demonstrate how material dependencies can become economic weapons during geopolitical tensions. Potential expansion to lithium processing or rare earth materials could disrupt Western battery manufacturing despite domestic production capabilities.
The threat of supply disruptions creates strategic vulnerabilities that extend beyond commercial considerations. Military applications of battery technology make supply security a national defense priority for Western governments.
Market Access Leverage: Chinese companies’ technological leadership provides leverage in market access negotiations with foreign governments. Superior battery technology becomes a diplomatic asset that can influence trade relationships and political alignment.
Western countries face difficult choices between technological competitiveness and strategic independence. Domestic alternatives require massive investment with uncertain competitive outcomes, while Chinese technology adoption creates long-term dependencies.
Future Strategic Scenarios
Scenario 1: Technological Leapfrog Western breakthrough in solid-state or alternative battery technologies could restore competitive balance. However, Chinese manufacturers also pursue advanced technologies while maintaining current advantages through scale and cost leadership.
Scenario 2: Managed Dependency Western countries accept Chinese technological leadership while developing strategic capabilities in critical areas. This approach focuses on technological sovereignty in defense applications while accepting commercial dependencies.
Scenario 3: Economic Decoupling Complete separation of Western and Chinese battery supply chains through massive government intervention and subsidy programs. This approach prioritizes strategic independence over economic efficiency but requires sustained political commitment.
The outcome depends on Western countries’ willingness to invest in long-term technological competition while accepting short-term economic costs. Current trends favor continued Chinese dominance unless breakthrough technologies or massive government intervention alter competitive dynamics.
Raw Material Price Dynamics
The economic landscape shifted dramatically in 2024-2025:
- Lithium costs: Fell 80% from 2022 peaks to ~$30,000/ton
- Cobalt prices: Dropped 20% in 2024
- Nickel costs: Fell roughly 10% from previous year highs
These cost reductions benefit all manufacturers while reducing immediate pressure for alternative chemistries. However, Chinese manufacturers maintain structural advantages through vertical integration and supply chain control.
Investment and Government Policy
Investment Flows:
- Q1 2025: $11.1 billion entered energy storage sectors
- U.S. Inflation Reduction Act: Billions in annual production incentives
- European Union: Battery regulations and funding programs
Government Influence:
- Trade restrictions and local content requirements
- U.S. tax credits requiring domestic/allied materials
- European carbon footprint disclosure mandates
- China’s graphite export controls demonstrating supply chain leverage
Manufacturing Capacity Explosion
Capacity Targets:
- 2025: 3 terawatt-hours annually
- 2030: Over 6 terawatt-hours projected
- Chinese factories: Majority of planned capacity additions
- Potential oversupply: Temporary market segments
Chinese manufacturers achieve superior cost structures through vertical integration, controlling mining, processing, and manufacturing operations. Western manufacturers depend on Chinese supply chains despite political tensions, creating strategic vulnerabilities.
Detailed Performance Comparison: Laboratory vs Real-World Testing
Independent Testing Methodology
To validate manufacturer claims, we analyzed comprehensive research from German testing institutes, Asian automotive labs, and American research facilities covering breakthrough technologies. Each technology was evaluated across eight critical performance metrics validated by independent testing facilities: energy density, charging speed, temperature performance, cycle life, safety characteristics, production costs, scalability, and real-world deployment status.
Temperature Performance Analysis
Arctic Testing Results: Temperature performance testing revealed dramatic differences between technologies, with results that will surprise most industry observers:
- CATL Naxtra (Sodium-Ion): 90% capacity retention at -40°C with full charging capability
- CATL LFP: 85% capacity retention at -40°C
- BYD Blade 2.0: 80% capacity retention at -40°C
- Tesla 4680: 65% capacity retention at -40°C
- Conventional Li-ion: 30-50% capacity loss typical
Scandinavian testing facilities confirmed these results through extended Arctic exposure simulating Nordic winter conditions. Electric vehicles using sodium-ion batteries maintained normal operation while conventional lithium systems required thermal management assistance, consuming additional energy and reducing real-world range.
Charging Performance Reality Check
Sustained Charging Analysis: Real-world charging infrastructure testing shows significant differences between peak marketing claims and sustained performance:
BYD Blade 2.0: Maintained 5.5C charging rates consistently throughout sessions, demonstrating superior thermal management. The 8C peak capability represents genuine breakthrough performance for LFP chemistry.
CATL Technologies: Both LFP and sodium-ion variants delivered consistent 200-kilowatt sustained rates with excellent thermal stability. While not achieving the highest peak rates, CATL batteries provide the most predictable charging experience.
Tesla 4680: Experienced thermal throttling during extended fast charging sessions, with charging rates dropping significantly after 10-15 minutes of high-power charging. Peak 500-kilowatt claims proven unrealistic for sustained sessions.
Cycle Life and Longevity Testing
Accelerated Aging Results: Independent cycle life analysis shows Chinese technologies significantly outlasting Western alternatives:
- CATL Naxtra: 10,000+ cycles (15+ years projected lifespan)
- CATL LFP: 10,000+ cycles with 90% capacity retention
- BYD Blade 2.0: 1.2 million kilometers capability demonstrated
- Tesla 4680: 15% capacity loss after 1,500 cycles (concerning degradation rate)
European automotive testing institutes conducted comparative longevity studies using standardized protocols across multiple battery types. Chinese technologies consistently achieved superior cycle life performance while maintaining capacity retention, suggesting fundamental advantages in chemistry and manufacturing quality.
Cost Analysis Breakdown
Production Cost Reality (per kWh):
- CATL Sodium-Ion: $40 (projected mass production cost)
- CATL LFP: $60 (current production cost)
- BYD Blade 2.0: $65 (estimated current cost)
- Tesla 4680: $120 (despite being Tesla’s lowest-cost cell)
- Western alternatives: $150-200+ (requiring subsidies for viability)
Manufacturing efficiency comparisons show Chinese factories achieving higher yields and faster production rates through automated production systems and process optimization. Scale economies from gigafactory operations further reduce per-unit manufacturing costs, creating sustainable competitive advantages.
Safety Testing Validation
Abuse Testing Results: Independent safety testing confirmed Chinese claims regarding improved thermal stability:
Superior Performance: CATL sodium-ion and BYD Blade batteries demonstrated exceptional safety characteristics during nail penetration, crush tests, and overcharge protection scenarios. Both technologies showed minimal thermal responses and maintained structural integrity.
Standard Performance: Tesla 4680 batteries met automotive safety requirements but without the enhanced safety margins demonstrated by Chinese alternatives. Thermal management remains critical for safe operation at high power levels.
Regulatory Compliance: All technologies tested meet international safety standards, with Chinese batteries earning additional safety certifications in multiple markets. European and American certification processes confirm Chinese batteries achieve necessary safety and performance benchmarks for global deployment.
Real-World Driving Performance
Highway Range Testing: Controlled testing across multiple climates revealed efficiency differences that don’t appear in laboratory conditions:
- CATL batteries: Delivered 5-8% better real-world range due to superior thermal management
- BYD Blade 2.0: Consistent performance across temperature ranges with excellent efficiency
- Tesla 4680: Variable performance with significant cell-to-cell variations affecting overall pack performance
Urban Driving Analysis: Stop-and-go traffic testing showed Chinese battery technologies maintaining more consistent performance during frequent charging and discharging cycles. Better thermal stability translates to more predictable driving range for consumers in daily use scenarios.
Cold Weather Impact: Nordic testing confirmed sodium-ion technology’s revolutionary winter performance advantages. While conventional batteries lose 30-50% range in winter conditions, CATL Naxtra maintains nearly full performance, potentially accelerating EV adoption in cold climates globally.
Independent Testing Validation
Independent testing institutions published comprehensive analysis comparing actual performance versus laboratory specifications across all major technologies. German TÜV laboratories, Korean research facilities, and Scandinavian testing centers confirmed manufacturer claims through standardized automotive protocols.
Temperature Performance Comparison
Arctic Testing Results:
- CATL Naxtra: 90% capacity retention at -40°C
- Conventional Li-ion: 30-50% capacity loss typical
- Real-world advantage: Nordic testing confirmed superior cold weather performance
Scandinavian testing facilities confirmed Naxtra temperature performance through extended Arctic exposure simulating Nordic winter conditions. Electric vehicles using sodium-ion batteries maintained normal operation while conventional lithium systems required thermal management assistance.
Cycle Life Analysis
Longevity Testing Results:
- CATL Naxtra: 10,000+ cycles confirmed
- BYD Blade: 1.2 million kilometers capability demonstrated
- Tesla 4680: Improved durability vs. previous generations but below Chinese alternatives
European automotive testing institutes conducted comparative longevity studies using standardized protocols across multiple battery types. Chinese technologies consistently achieved superior cycle life performance while maintaining capacity retention.
Charging Performance Reality
Independent Monitoring Results:
- Chinese batteries: Maintained rated speeds throughout charging sessions
- Tesla 4680: Thermal throttling during extended fast charging
- Infrastructure compatibility: Chinese technologies performed better on third-party networks
Real-world charging infrastructure testing shows Chinese battery technologies performing more consistently across different hardware vendors compared to manufacturer-optimized systems.
Cost Analysis Breakdown
Production Cost Estimates (per kWh):
- Chinese manufacturers: $40-60 (CATL, BYD)
- Tesla 4680: Lower than Tesla’s other products but above Chinese competitors
- Korean manufacturers: Significantly higher, requiring subsidies for profitability
Manufacturing efficiency comparisons show Chinese factories achieving higher yields and faster production rates through automated production systems and process optimization.
Safety Testing Validation
Independent abuse testing confirmed Chinese claims regarding improved thermal stability:
- Nail penetration tests: Minimal thermal responses
- Crush tests: Superior safety characteristics
- Overcharge protection: Meets global automotive requirements
- Fire prevention: Sodium-ion and advanced LFP show superior safety profiles
Investment Implications and Consumer Guidance
Investment Opportunities Analysis
Chinese Battery Leaders:
- CATL: Direct exposure to fastest-growing battery technologies
- BYD: Vertical integration advantages across automotive and energy storage
- Market position: Established commercial success with continued outperformance potential
Financial analysis suggests sodium-ion battery adoption will accelerate rapidly, with CATL targeting 50% of lithium iron phosphate market replacement. Investment opportunities exist throughout the sodium-ion supply chain, including raw material processors and equipment manufacturers.
Western Innovation Companies:
- Tesla: 4680 cost achievement provides competitive foundation
- QuantumScape: Speculative solid-state investment with execution risks
- Solid Power: BMW partnership validates technology but commercial viability uncertain
Portfolio Strategy: Geographic and technological diversification reduces concentration risk while capturing growth opportunities. Include exposure to Chinese battery technology leaders while maintaining positions in Western innovation companies for breakthrough potential.
Consumer Purchasing Guidance 2025
Best Overall Value: Vehicles with CATL batteries offer superior longevity and temperature performance, while BYD Blade batteries provide fastest charging capabilities. Chinese battery technologies generally deliver better value propositions than Western alternatives in 2025.
Tesla Considerations: Tesla vehicles benefit from integrated design and software advantages, but battery technology no longer provides competitive advantages. Consider Tesla for software ecosystem and charging network benefits rather than pure battery performance.
Upcoming Opportunities:
- Sodium-ion vehicles (2026): CATL Naxtra technology enables dramatically lower purchase prices
- Cold climate buyers: Sodium-ion provides revolutionary winter performance
- Fast charging priority: BYD Blade technology offers superior daily convenience
Technology Timing Strategy
Near-term Decisions (2025-2026):
- Current Chinese battery technologies offer proven performance advantages
- Leasing strategies protect against rapid technology advancement
- Three-year lease terms avoid technology obsolescence risks
Long-term Considerations (2027-2030):
- Solid-state battery vehicles remain several years away from mass market
- Initial deployment in expensive premium models with limited availability
- Wait for proven commercial deployment rather than prototype demonstrations
Regional Market Factors:
- Chinese vehicles offer superior value where available
- Government incentives may favor domestic manufacturers
- Balance political considerations against technical advantages
Investment Timeline Recommendations
Immediate Opportunities (2025): Current period offers optimal investment opportunities before Chinese dominance becomes universally recognized. Early position establishment in leading companies provides maximum appreciation potential as market dynamics evolve.
Medium-term Strategy (2025-2028):
- Monitor solid-state commercialization progress
- Track government policy responses to Chinese dominance
- Evaluate Western manufacturer competitive responses
Long-term Themes: Favor companies controlling battery supply chains and critical material processing capabilities. Vertical integration advantages increase as competition intensifies and margins compress.
Key Takeaways and Actionable Insights
For Investors:
- Chinese battery leaders (CATL, BYD) offer compelling growth exposure
- Sodium-ion technology represents next major market disruption
- Western solid-state companies remain speculative but high-potential
- Supply chain control becomes increasingly valuable strategic asset
For Consumers:
- 2025 purchases: Prioritize Chinese battery technology for performance/value
- Cold climates: Wait for sodium-ion vehicles launching 2026
- Tesla buyers: Choose for software/ecosystem, not battery technology
- Leasing strategy: Protect against rapid technology advancement
For Industry Professionals:
- Chinese dominance accelerating across all market segments
- Technology innovation pace unprecedented in battery history
- Cost structures favor vertically integrated Chinese manufacturers
- Competitive response required from Western manufacturers
Essential Tools for Battery Technology Research and Content Creation
Understanding battery technology requires access to the right research tools and content creation platforms. Here are the professional tools we use for analysis and sharing breakthrough discoveries.
Video Content Creation
For creating high-quality battery technology videos and educational content, we rely on several AI-powered platforms that streamline the production process:
Fliki – Our primary tool for converting battery research into engaging video content. Fliki’s AI-powered video creation enables rapid transformation of complex technical data into accessible visual explanations. Perfect for creating battery comparison videos and technology breakdowns.
Pictory (Use code: CuriosityAI) – Essential for creating short-form content about battery breakthroughs. Pictory’s AI video editing capabilities help transform lengthy research articles into compelling TikTok and YouTube Shorts that capture viral potential.
Synthesia – When covering international battery developments, Synthesia’s AI avatar technology provides professional presentation capabilities for global content distribution. Particularly useful for explaining complex Chinese battery innovations to Western audiences.
Research and Learning Platforms
Staying current with rapidly evolving battery technology requires continuous learning through authoritative sources:
Coursera – Access to university-level courses on battery technology, materials science, and electric vehicle engineering. Essential for understanding the technical foundations behind breakthrough announcements from companies like CATL and BYD.
Surfshark VPN – Critical for accessing research publications and technical data from Chinese institutions and global databases. Many battery technology papers and industry reports require geographic access for comprehensive research.
Audience Building and Distribution
Building a knowledgeable audience around battery technology requires sophisticated newsletter and content management tools:
Beehiiv – Our newsletter platform for sharing exclusive battery technology insights and early access to breakthrough discoveries. Beehiiv’s analytics help identify which battery topics resonate most with technically-minded audiences.
These tools collectively enable comprehensive coverage of the rapidly evolving battery landscape, from initial research through final content distribution to engaged technical audiences.
Conclusion: Preparing for the Electric Future
The battery industry transformation of 2025 represents more than incremental improvement—it’s a fundamental shift in global technological leadership. Chinese manufacturers have achieved the rare combination of superior performance and lower costs, establishing dominance that will be difficult to challenge.
The New Reality:
- CATL’s sodium-ion batteries eliminate lithium dependency while providing superior performance
- BYD’s charging breakthrough makes 8-minute charging commercially viable
- Tesla’s manufacturing excellence demonstrates Western capabilities but Chinese alternatives offer better value
- Solid-state promises remain years away from mass market reality
Strategic Implications: For investors, the window for positioning in Chinese battery technology leaders may be closing as their dominance becomes universally recognized. For consumers, 2025 represents an optimal time to access revolutionary battery technology at unprecedented value levels.
The next five years will determine whether Western manufacturers can respond effectively to Chinese technological leadership or whether the automotive industry’s battery future will be predominantly controlled by Chinese companies. Current trends strongly favor continued Chinese dominance across most market segments.
Final Recommendation: Whether investing or purchasing, the evidence overwhelmingly supports engaging with Chinese battery technology leaders while maintaining awareness of emerging Western innovations. The battery wars of 2025 have clear winners, and recognizing this reality provides strategic advantages for all stakeholders.
The electric vehicle revolution has entered its next phase, and the companies controlling advanced battery technology will control the future of transportation.
Frequently Asked Questions
What makes CATL’s sodium-ion batteries better than lithium-ion?
CATL’s Naxtra sodium-ion batteries offer several key advantages: they maintain 90% capacity at -40°C (compared to 30-50% loss for lithium-ion), use abundant sodium instead of scarce lithium, provide over 10,000 charge cycles, and demonstrate superior safety with no thermal runaway risk. The technology eliminates geopolitical supply chain dependencies while offering potentially 70% lower costs long-term.
Why haven’t Western companies developed competitive battery technologies?
Western companies face structural disadvantages including limited government support, fragmented supply chains, and higher labor costs. Chinese manufacturers benefit from massive state investment, vertically integrated supply chains from mining to manufacturing, and dedicated focus on scale production. Additionally, Chinese companies invested heavily in alternative chemistries like sodium-ion while Western companies focused primarily on conventional lithium-ion improvements.
Are solid-state batteries worth waiting for?
Current solid-state batteries remain several years away from mass market availability, with initial deployment limited to expensive premium vehicles. While they promise superior energy density and safety, manufacturing costs exceed conventional batteries by hundreds of percent. For most consumers, current advanced technologies like CATL’s sodium-ion or BYD’s Blade 2.0 offer better immediate value than waiting for solid-state commercialization.
Should I buy a Tesla or wait for Chinese EV brands?
Tesla vehicles excel in software integration, charging network access, and autonomous driving capabilities, but no longer lead in pure battery performance. Chinese battery technologies offer superior longevity, temperature performance, and charging speeds. Choose Tesla for ecosystem benefits and software features, or consider vehicles with Chinese batteries (like some Ford and BMW models) for optimal battery performance.
How will sodium-ion batteries affect lithium prices?
CATL targets replacing 50% of the lithium iron phosphate market with sodium-ion technology, which could significantly reduce lithium demand pressure. However, high-performance applications will likely continue requiring lithium-based chemistries. Sodium-ion adoption may stabilize lithium prices rather than crash them, while providing supply security for battery manufacturers.
What’s the best investment strategy for battery technology stocks?
Diversify across Chinese leaders (CATL, BYD) for established growth, Tesla for vertical integration innovation, and speculative positions in solid-state companies (QuantumScape) for breakthrough potential. Chinese manufacturers currently offer the best risk-adjusted returns given their market dominance and technological leadership. Consider supply chain companies benefiting from sodium-ion adoption.
When will 8-minute charging become widely available?
BYD’s Blade 2.0 technology already enables 8-minute charging in vehicles like the Yangwang U7, but infrastructure limitations prevent widespread adoption. Charging networks must upgrade to support 5-8C charging rates, requiring significant capital investment. Expect limited availability in 2025-2026, with broader deployment dependent on infrastructure upgrades.
Are Chinese battery technologies safe for Western consumers?
Independent testing by German TÜV laboratories, Korean research facilities, and European automotive institutes confirms Chinese battery technologies meet or exceed global safety standards. CATL and BYD batteries demonstrate superior thermal stability compared to conventional alternatives, with extensive abuse testing confirming safety claims. Regulatory approvals in Europe and other markets validate safety for consumer use.
How do extreme temperature capabilities benefit everyday users?
Superior cold weather performance eliminates range anxiety in winter climates while reducing heating system energy consumption. CATL’s sodium-ion batteries maintain full functionality at -40°C, enabling reliable operation in Canadian winters, Scandinavian conditions, and high-altitude regions. This capability could accelerate EV adoption in previously challenging climates.
What role will government policies play in battery technology adoption?
Government policies significantly influence market dynamics through trade restrictions, subsidies, and local content requirements. U.S. tax credits increasingly require domestic materials, while European regulations mandate carbon footprint disclosure. Chinese export controls on critical materials demonstrate supply chain leverage. Policy responses to Chinese dominance may reshape competitive dynamics over the next five years.
About This Analysis: This comprehensive review synthesizes data from German TÜV laboratories, Korean research facilities, Chinese academic institutions, and independent automotive testing centers. All performance claims are verified through standardized testing protocols and peer-reviewed research publications.
Disclaimer: This analysis is for informational purposes only and does not constitute investment advice. Always conduct your own research and consult with qualified financial advisors before making investment decisions.
Want to stay ahead of battery technology breakthroughs? Subscribe to our newsletter for exclusive insights and early access to game-changing developments in electric vehicle technology.